
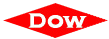




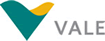

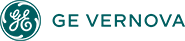






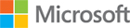
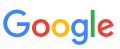

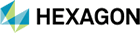


While the disruptive and costly impact of downtime, especially unplanned downtime, is by now largely understood, the reactive nature of conventional maintenance strategies used in most plants remains inadequate for maintaining maximum equipment uptime and ensuring continuity of production.
This was the backdrop to the March 26 Digital Transformation Council (DTC) Asia webinar, Advancing Plant Asset Management with IoT Technology, which, helmed by guest speaker representation from Azbil Corporation Southeast Asia office in Singapore, sought to explore how IoT technologies and online service capabilities are enabling companies to transform maintenance of control valve assets, in particular, through much earlier detection of abnormalities, and so helping to achieve safe, stable and environmentally sustainable operations.
In his introductory presentation, Bob Gill, General Manager, Southeast Asia, ARC Advisory Group, reminded the online audience of ARC’s research over many years on the impact of downtime on industrial operations and that unplanned downtime, especially, continues to be a serious issue, as evidenced by recent news headlines highlighting major incidents in the downstream oil & gas sector across Asia.
“Aside from the extensive disruption, what comes through when you read these kinds of stories is the considerable financial impact from these incidents,” he said. As well as from costs directly related to the lost production, the impact is felt from additional labor and inventory costs associated with repair and replacement, and in customer issues such as delayed deliveries. And the more critical an asset is to operations, the greater the impact of any sudden failure.
Companies looking to increase the reliability of their plant assets are potentially in a much better position than they were a decade ago thanks to the advances in and increasing availabilities of digital technologies, notably in the form of Industrial IoT. This judicious combination of sensors, edge computing, connectivity, and data analysis enables real-time remote monitoring of equipment status and access to value-added information about the health of an asset by different parties, including the original product supplier and the customer.
Accordingly, with Industrial IoT, manufacturers can evolve the conventional business model of supply of products plus some basic after-sales services to one centered around a much higher and more sophisticated level of service through being able to stay connected to the asset once it is out and operating at the customer site. And so enabling a transition from the traditional product transaction to a much deeper relationship with the customer – where the services component is a more significant portion of the offering.
The presentation concluded by highlighting several success factors for control valves adoption that have been identified through ARC’s extensive market research on the technology, which is worth close to $7 billion annually, with a significant services component included in that amount. Several of those factors relate to improving the reliability of installations though, among other aspects, deployment of remote monitoring services, encouraging the adoption of new technologies and work processes, and partnering more closely with product suppliers to ensure optimum system performance.
In his presentation, Overcoming Operational Challenges with Control Valve Maintenance Support System, Darwin Kusuma, Regional Technical Sales Specialist at Azbil’s Strategic Planning & Development Office for Southeast Asia in Singapore, picked up on some of the themes introduced by ARC to illustrate how condition based maintenance (CBM) of control valves allied with digital technologies can bring real benefits to industrial companies through all phases of the plant lifecycle – startup, operations, and scheduled turnarounds.
“A pressure control valve may seem to operate normally. But when it gets stuck and fails to open, it can quickly become critical because the system upstream will be over pressurized. In such a case, isn’t it better to detect the problem early before it causes an unprecedented emergency?” he asked.
“You also need to maintain the control valves to keep them in optimal working condition. But how do you determine which valves to overhaul? In conventional time-based maintenance (TBM), you may find that some valves are still in good condition even if they are due for maintenance. But in fact, maintenance is not needed yet. On the other hand, some other valves may already be in critical condition, but they do not get overhauled until the next schedule.”
The Control Valve Maintenance Support System is anchored on a HART-enabled Azbil smart valve positioner, which is attached to a control valve and provides multiple sensed diagnostic parameters, such as stick-slip and total stroke. Through data analysis and interpretation by Azbil experts, early warning of issues like sticking or galling due to scale accumulation or wear and tear of gland packing/bellows and actuator parts becomes possible. The smart valve positioner can be deployed to both Azbil and non-Azbil control valves in a facility.
A chemical company in Japan installed Azbil’s Control Valve Maintenance Support System with a view to reduce maintenance costs and increase product competitiveness. As Darwin Kusuma articulated, on one occasion, a problem in the plant’s hydrogen unit was indicated by activation of the hydrogen pressure alarm, but the root cause could not be determined. Using the Control Valve Maintenance Support System, the customer performed a step response test and found that the hydrogen pressure control valve was hunting. After overhauling the valve and reinstallation, the valve stopped hunting and the hydrogen pressure stabilized. Had the cause not been detected, the operation of the plant could have been adversely impacted.
Following the presentations, an engaging panel session featuring ARC and Azbil elaborated and clarified on the key themes presented. This can be viewed along with the rest of the Digital Transformation Council (DTC) Asia webinar via the You Tube video at Advancing Plant Asset Management with IoT Technology