




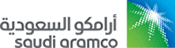

Field service involves widely distributed assets and requires features like integrated maps, route optimization, in-vehicle parts inventory management, and customer billing. Field Service Management (FSM) solutions are typically designed for use by third parties that provide maintenance services to asset owners and operators. In some cases, FSM is used for self-service of assets–notably electric power transmission and distribution.
FSM systems plan, optimize, execute, and track the needed service activities including the associated priorities, skills, materials, tools, and information. For FSM, financial management extends into order management that includes credit approval, order entry, and billing after service delivery to customers.
Key product areas and functional categories include:
Service order management including mobility
Purchasing and inventory management for parts
Billing and financial management
Labor skills management
Reporting and Analytics
Service contract management
Service order management including mobility: Service order management covers the work performed by or managed by the field service organization. This includes the processes, technology, and information related to the work order creation, planning, scheduling, schedule optimization, execution, documentation, and tracking of activities. Here, mobility provides a means for technicians to process their work orders while they are doing the work in the field.
Creation includes generation and receipt of work requests, analysis of requests in terms of cost, impact and warranty coverage, management of the approval process, and dissemination of requests to appropriate parties.
Planning includes long-term planning of work activities based on resource availability and activity precedence requirements.
Scheduling includes the assignment of specific resources and time slots to individual work order tasks.
Optimization of scheduling includes enhancing (in an automated way), the work order assignments for high efficiency or response time given the current labor or material constraints.
Execution includes dissemination of work tasks to appropriate resources and tracking of progress.
Documentation covers the creation of records throughout the work order lifecycle. This includes the work assignments, work accomplished, resources expended, when performed, problems, lessons learned, final equipment state/status, and more.
Tracking provides visibility for the status of work order requests, work orders, and work progress throughout the work order’s lifecycle.