
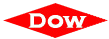




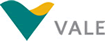

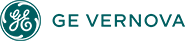




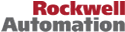

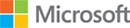
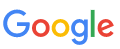

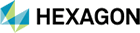


Keywords: Open Digital Twin, ExxonMobil, Interoperability, Reality Capture, Asset Visualization, Data Governance, Plug-and-play, Vendor Agnostic, Virtual Assembly, ARC Advisory Group.
At the recent ARC Industry Forum in Orlando, the session on “Digital Twin Journey Through Visualization, Data Literacy and Standards” brought forth interesting perspectives on the value of open digital twins and an ecosystem and need for open standards. Nick Peterson, the 3D product owner for ExxonMobil responsible for scaling and sustaining digital twins across ExxonMobil sites, clearly articulated the company vision for a Digital Reality Ecosystem (DRE).
Rooted in the Exxon DRE are a set of very strategic elements: capture, storage, delivery, consumption, and data governance. Through this approach ExxonMobil is working to separate data and software, achieve interoperable file formats, and build a 3D central storage repository with partners. The vision will be a variety of consumption tools provided by portals to information for use cases such as maintenance planning, turnaround planning, and engineering design.
ExxonMobil has established guardrails and best practices for reality capture, to ensure seamless ingestion of data into their consumption platforms and calling for industry standards for engineering CAD models. Through these data strategies they are pushing for lower-cost reality capture methods and aim to scale digital twins around the world with fully embedded and contextualized data foundations with virtual assembly and additive manufacturing as key investment areas.
ExxonMobil has a digital reality ecosystem that consists of four pillars: capture, storage, delivery, consumption, and data governance. They are working with providers to separate data from software and achieve interoperable file formats for use on any platform. They are also working with AWS to build a 3D central storage that is API-driven for sending data to any consumption tool. Consumption tools, such as augmented reality, virtual reality, laptops, tablets, and phones, are portals to information. The actual use cases include maintenance planning, turnaround planning, engineering design, project design, and construction progress monitoring.
The foundation of DRE includes the following principles:
Democratize the capture.
Separate data and software
Storage will be independent from consumption.
Allow plug-and-play and agnostic integration.
Enable rapid innovation, value creation, and data reuse anytime, anywhere.
Create a digital thread to enable tracking what, where, when, why
The DRE is standards-based, open, secure, and interoperable data platform with a future state to encourage digital consumption and many use cases.
ExxonMobil has been focusing on two mature use cases: virtual assembly and additive manufacturing. Virtual assembly involves virtually fitting up equipment or components to reduce rework and save time and money on turnarounds. Additive manufacturing involves scanning parts to a high degree of accuracy and 3D printing them. The company is working with an industry consortium called Fieldnode on additive manufacturing and has a team dedicated to virtual assembly and additive manufacturing. They are also working on using visual data and source data from systems like SAP to improve turnaround and maintenance planning and enable remote planning by giving technical centers and engineering groups access to the same data as people at the site.
Virtual assembly is one of the mature use cases that ExxonMobil has been focusing on. It involves virtually fitting up equipment or components to reduce rework and save time and money on turnarounds. This is achieved by scanning the area where the equipment or component will be placed and giving the data to an engineering company for detailed design. The fabricator then fabricates the equipment or component, and it is virtually fitted before it gets to the site. By reducing rework, Exxon can save a significant amount of time and money on turnarounds.
Additive manufacturing is a process that involves creating three-dimensional objects by building up layers of material, such as plastic or metal. They have a team dedicated to both virtual assembly and additive manufacturing, and they are teaching users at their sites how to perform quality assurance and quality control on the data. The process involves scanning parts down to a 1,000th of an inch and putting them into a digital inventory. Then, the part can be 3D printed, whether it's an impeller on a pump or something else.
Data is key to Exxon's digital reality ecosystem. They are working on getting data standards and contextualization correct, linking data from systems like SAP and reliability systems. On the 2D side, they are looking at industry standards like DEXPI to create sustainable models for P&IDs, inspection isometrics, and other drawings. They aim to be interoperable with any software they choose to use. On the 3D side, they need to be able to deliver different ways for users to visualize information, such as reality capture scans, 3D engineering CAD models, and panoramic pictures. This requires working with an ecosystem of suppliers and vendors to deliver the entire solution.
Exxon has been delivering several use cases this year. The first use case is navigation and familiarization, which involves using 3D scans, laser scans, photogrammetry, or mobile scanners to give remote users access to the site. This can be used for technical centers, equipment strategies, remote planning, or virtual reality training scenarios. In its simplest form the reality capture model provides a point cloud / mesh 3D model of the unit that can be navigated by users. 360 Images that were taken by ground-based equipment can be viewed and navigated like “Google Earth”. Images from drones are also placed geospatially and can be viewed for the top-down view of the assets.
The second use case involves overlaying 2D with 3D to visualize firewater systems, sewers, underground lines, and other systems. Heritage 2D drawings take on new value when placed on top of 3D reality capture. Possibilities are endless such as overlaying unit plot plans with scans of unit to essentially label the assets in 3D. This can reduce the need for users to go into the field to walk down these lines.
The third use case is planning and scoping, which involves using detailed design data in engineering authoring tools. The data can be exported into a neutral file format for use by anyone. This can be used for simple measurements, mockups, and logistical planning. Dimensioning capabilities are essential to enhanced Turnaround planning and logistics as well as design, troubleshooting, and much more. At a site, a design draftsman worked full time getting elevations for SRR studies. Now any elevation can be achieved with a single click of a mouse.
ARC Advisory Group clients can view the complete report at the ARC Client Portal.
Please Contact Us if you would like to speak with the author.
Obtain more ARC In-depth Research at Market Analysis