
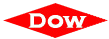




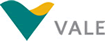

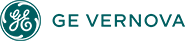




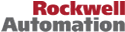

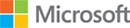
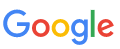

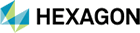


Information technologies (IT) have been influencing industrial automation systems ever since the advent of Industry 4.0 over a decade ago. This initiative taught risk averse industry players the value and benefits of using “IT-like” architectures, for example, to tap into raw process data for continuous optimization. It also created a data-driven vision of the future where products and production processes are modeled and tested using digital twins. The “IT-ification” of automation architectures started with Ethernet-based industrial networks and led to the creation of the industrial edge, the space on the factory floor where classic automation meets the IT world. As the trend continues, we are now witnessing the migration of real-time control from dedicated hardware to a managed IT environment.
In a big step for the market leader, Siemens has launched its first virtual programmable logic controller (vPLC), the Simatic S7-1500V. This ARC View looks at the advent of software-defined automation at the controller level and its impact on the way automation systems will be engineered, deployed, and managed in the future.
Key Takeaways
The vPLC will not entirely replace the dedicated hardware of the classic PLC. Instead, the two will coexist indefinitely as users decide to deploy each solution where it fits best.
In a containerized software environment, the vPLC offers many advantages over the classic PLC in areas such as ease of deployment, manageability, scalability, and flexibility. However, benefits will be realized only when users migrate to truly IT-like architectures and train staff to design and operate them.
The vPLC is just one part of an end-to-end solution for an automation architecture that also includes the infrastructure, machine apps, and third-party components.
Siemens is not new to software-defined automation. The company has for years marketed a soft PLC bundled with an industrial PC, and now offers the Siemens Industrial Edge, a platform for the integration of IT and OT. What’s different about the new Simatic S7-1500V virtual PLC is the deployment. The vPLC is purchased and downloaded like an app, and then installed and integrated in the edge environment. Siemens leaves the choice of the hosting hardware up to the user (but provides a list of reference hardware). Otherwise, the new vPLC is no different in functionality from classic Siemens PLCs.
Data centers were the pioneers of virtualization. Before virtualization, data centers consisted of dedicated function servers running a single application (database, email, file sharing, CRM, ERP). Each server had to be individually administered, configured, and scaled to support the maximum demand placed on its application or service. Virtualization greatly reduced the number of physical servers required, lowered energy consumption, and provided better visibility and manageability of IT operations. Server virtualization was the first step toward today's software-defined data center and cloud computing infrastructure.
Industrial automation technology is following a similar path. For automation solutions, this transformation means consolidating multiple automation functions such as visualization, production management, or batch control in virtual machines running on a common hardware and software platform (a plant server). While electromechanical devices like sensors, actuators, and motors remain on the machine, the traditional function of the PLC installed in the electrical cabinet is now virtualized in a container and deployed on the plant server, close to other software. To the machine operator, the day-to-day function of the automation system should remain the same, but maintenance personnel may have to learn new skills to deal with operational issues.
The concept of the virtual PLC raises a myriad of questions. Is the vPLC a drop-in replacement for the classic PLC? How does performance compare? Which applications will remain the domain of the classic PLC? What new opportunities does the vPLC create? Below are descriptions of potential benefits and caveats of the vPLC.
A vPLC is purchased in an app store, downloaded, and then deployed in a container at the industrial edge. Edge platforms typically support apps and devices from an ever-growing ecosystem of products and solutions, including from third parties. Dedicated platforms like the Siemens Industrial Edge offer the tools for deploying and monitoring the performance of automation assets and services that allow apps and devices to communicate easily with one another while maintaining a small footprint.
While traditional PLCs are deployed manually, often with manually set parameters, vPLCs are deployed like IT assets via “orchestration” – the process of automatically configuring, provisioning, and managing assets using common IT tools. After learning certain IT skills, automation engineers can deploy and monitor whole fleets of controllers across machines, lines and entire plants in a mixed configuration of software-defined and physical devices. A large manufacturing plant today may encompass several hundred PLCs, so the potential cost saving possible with centralized management of automation assets is huge.
While most machine builders would prefer to deliver machines with identical configurations and PLC programs, in reality, even standard machines are often modified to satisfy customer wishes and requirements. The vPLC offers machine builders several advantages: While classic PLC hardware is offered in different sizes and capacities, a vPLC comes in only one “model” that can be scaled up or down to meet the requirements of each machine.
A vPLC runs on a server, and users can reduce capital costs if multiple vPLCs are installed on a single hosting device. Interestingly, Siemens does not bundle the S7-1500V with industrial PCs. Instead, the choice of hosting hardware is left to the user, which puts the onus on the user to ensure that application requirements are met. However, support for this is provided by the Siemens Industrial Edge, which helps the user understand and manage PC resources.
So how many vPLCs can be installed on a server and what are the limits? Sources have suggested that a computing cluster of 10 to 20 vPLCs per server is realistic, but this depends on what the vPLCs are doing. Hard motion control with deterministic performance is the make-or-break test for PLCs. According to Siemens, the S7-1500V performs standard motion control tasks like its hardware-based brethren, but for advanced motion control (coordination of multiple servo axes), the company recommends a classic PLC and the use of a dedicated technology module (T-CPU).
vPLCs make automation systems more flexible and scalable. System size can be scaled up or down simply by changing the number of vPLC instances in use rather than by installing or removing hardware. Users pay only for controllers currently used -- an attractive model for machine builders that construct and ship machinery on a regular basis.
Virtualized systems are “orchestrated,” meaning that applications and devices can be deployed quickly via automated tasks for provisioning and configuration. This allows whole fleets of software-defined automation systems, smart devices and supporting applications to be deployed, monitored and managed efficiently using common tools.
Machine builders have invested huge sums in the development of PLC code, so it is no coincidence that vPLCs typically support legacy code and data structures, allowing users to leverage their existing IP and familiar engineering tools. For example, the Simatic S7-1500V is configured just like a traditional PLC with Siemens TIA Portal, so users can continue to use existing code developed for generations of Siemens PLCs. This also works in the other direction: users can easily switch back to a classic PLC if desired to mitigate any risk of changing and to support step-by-step roll outs.
The virtual PLC is deployed at the industrial edge - the space where new and legacy automation systems are integrated in an IT environment. For example, the Simatic S7-1500V runs in the Siemens Industrial Edge where applications and devices can be monitored centrally, in a common environment that fosters openness and data sharing with a long list of associated benefits. For example, users can operate and maintain manufacturing equipment with data-driven insights that can help optimize processes and even predict unexpected stoppages and breakdowns before they happen. These capabilities can be further enhanced by other apps, such as Profinet monitoring, running on the same edge platform.
Is an automation system that uses a vPLC less expensive to purchase than a traditional automation system? How do the lifecycle costs compare with those of a traditional PLC system? The jury is still out on a cost comparison of virtual versus classic PLC. While a vPLC still requires hardware to run on, users can deploy multiple instances of vPLCs on a single server, which reduces the overall device count and saves cabinet space. However, a vPLC just replaces the CPU of an automation system. IO modules, sensors, actuators and operator panels are still necessary, and these can make up the majority of the total system cost.
Additional cost savings can be realized through lower engineering costs achieved with a DevOps approach to lean software development that shortens development time while ensuring code quality and consistency.
While the virtual PLC is a new development in the otherwise mature market for discrete control, the advent of the virtually deployed controller is part of the bigger picture of an industry in the midst of a digital transformation. As use cases emerge, the business case for deploying automation systems in an IT environment will become more compelling.
The vPLC follows the long-established IT trend of “doing it in software if possible” but applies this trend to critical real-time control. The point of the vPLC is not to replace the classic PLC, but rather to deploy and manage the PLC function in a datacentric environment with all the benefits of modern IT tools and developments.
ARC Advisory Group clients can view the complete report at the ARC Client Portal.
Please Contact Us if you would like to speak with the author.
Obtain more ARC In-depth Research at Market Analysis